Here's a little writeup I did in Evans performances' subforum back on old hmt. Not tech, but it's something to add.
Ok, here's everything you need to know about springs. Note: Some of these numbers are estimates so all the calculations are rough, not exact. Also some are arbitrary guesses and work because the change in the number is what matters, not the actual numbers. (IE- 9-7=2 or 6-4=2, still a difference of 2)
Background: Springs push and pull. A spring's stiffness, k, is measured in mass/unit length. So say a spring has a spring constant of k=60 lbs/in. That spring will require 60 lbs to compress (or stretch) it an inch. If you want to compress it 2", 120 lbs will be needed. The force, F, a spring applies is: F=-k*x where x is you much you compress it. The more you compress it, the more it pushes. This relationship is linear.
Natural length- how long the spring is with no forces acting on it. It's unstretched, uncompressed length.
Coil bind length- The length of the spring when you compress it until the coils finally hit each other.
When building a spring, there are several things that contribute to how stiff it is. How wide the spring is, how many coils it has, the diameter of the wire used to construct the spring, the alloy of the steel used, etc.
Now my BOV's spring was too stiff. Thing didn't want to open and I was getting compressor surge. So I needed a softer spring. Well, reading up everybody either buys a new one for $$$ or cuts their old one. I had a feeling cutting it wasn't the "right" way to do it. It's not.
To make a spring softer, you need to either:
Increase the number of coils
Increase the width of the spring (how big around it measures, outer diameter)
Decrease the diameter of the wire.
Of course if you buy a softer spring, it will be the same length and width as your original, but will made of a smaller diameter wire.
Cutting the spring actually makes the spring stiffer, not softer. The opposite of what you want. Making it shorter reduces the number of coils you have. Only reason it "helps" is because it doesn't get compressed as much as before as it's now shorter.
For example, my stock spring in my Tial Style BOV measures:
4.108" long
1.510" O.D.
Wire diameter of 0.140"
8 coils
When you install the spring, it gets compressed to about 2.00" long. When the valve opens, it gets compressed to about 1.50" long. Let's ASSume that the k value for my stock spring is 42 lbs/in. This is only an approximation, but a few different derivations based on other info suggest this number is correct.
So, stock spring is pushing on the piston with a force of F=-k*x. Our k is 42 and our x is 4.108-2.00"= ~2.11". F= (42) (2.11) = ~ 89 pounds.
My motor pulls about -10.6 PSI at idle. I guestimated (read, forgot to measure) the area of the piston as 8 in^2. So when I'm at idle, the force from the diaphragm is (-10.6) (eight) = ~85 lbs.
The net force acting on the piston at idle is 89-85= 4lbs. So it's staying shut with 4lbs to spare. Those 4lbs are the problem. Ideally, the piston would be on the verge of opening at idle such that the slightest pressure difference when I shift will cause it to open.
Let's backpedal and figure out what value k we need. Ideally the net force acting on the diaphragm at idle will be close to zero, and not negative (if it's negative, the BOV begins to open and leak). Rearranging our equation and solving for k I get k_ideal = 40.2. This should be the ideal k as to keep the piston shut, but neutral at idle.
So time to make your spring softer. How? I ground on the coils. This effectively reduces the diameter of the coils, which makes the spring softer. Did this with a right angle grinder. It's easy, just hold the spring and grind a little flat on the spring. Do a spot, then turn it a 1/4 turn and do that spot, wash, rinse, repeat. I had to wet the spring a few times as it gets too hot to hold.
So how much do you grind off? Here's how I did it. I measured the OD of the wire to be 0.140". Well, I ground a bit on both sides of the coil. Measured the diameter between the flats in several places and the average was 0.120". However, that's only on two sides of the wire. I would say the effective diameter is 0.130" (because it measures .120 between the flat sides, and .140 between the round sides). So that would make for a (130/140) = 7.2% softer spring. Or if my original k was 42, my new k would be 39. That's lower than k_ideal though. And sure enough, damn valve leaks at idle now. At least the math agrees with my real world results. :l Should have only ground one side of the spring apparently. Actually, doing the math I should have only removed .012", not .020". However it barely leaks and I should be able to shim it to stop leaking so no worries. But had I done this math before, I would have got it right or closer the first time.
CLIFFS:
Spring too stiff? Grind on the coils to make it softer. Don't cut the spring, that's makes it worse.
Pictures for you visual folks:
I didn't have a vise, so I found a big hose clamp and some cardboard...
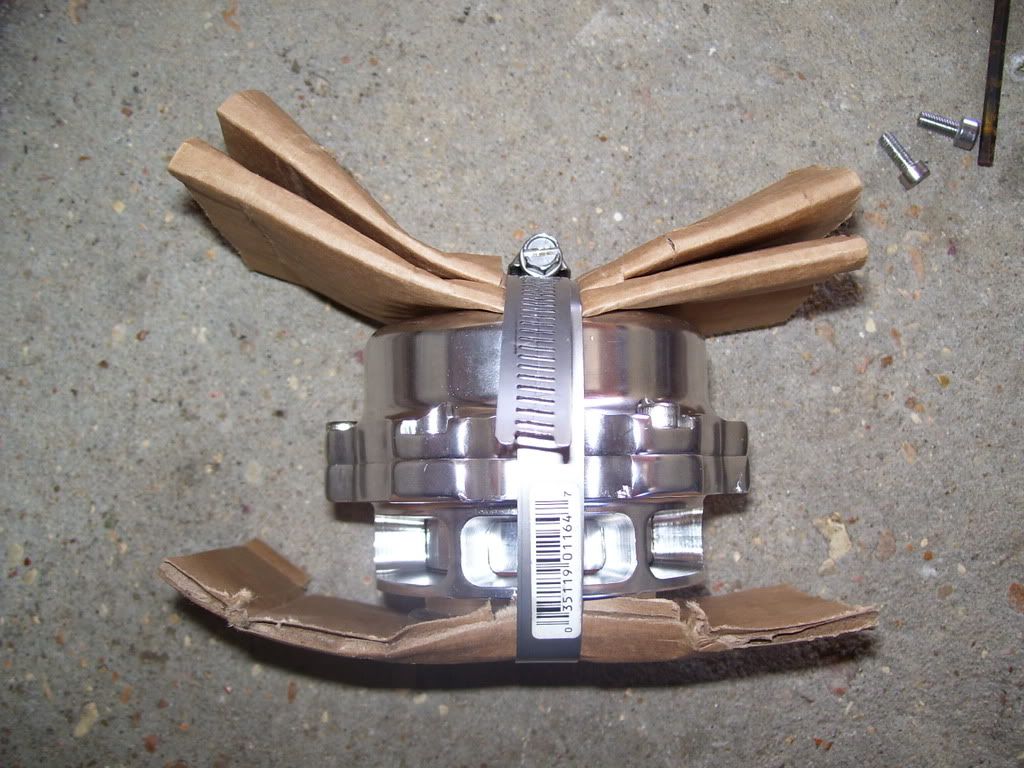
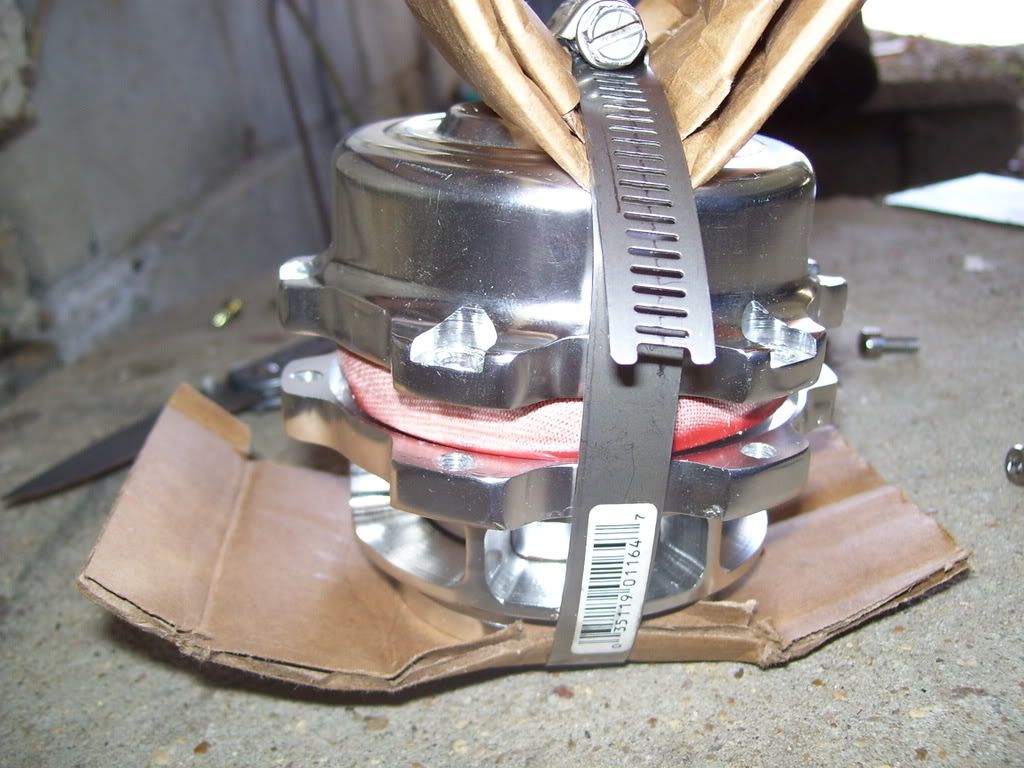
Measured the spring

Ground on that bitch

Pics of the BOV apart

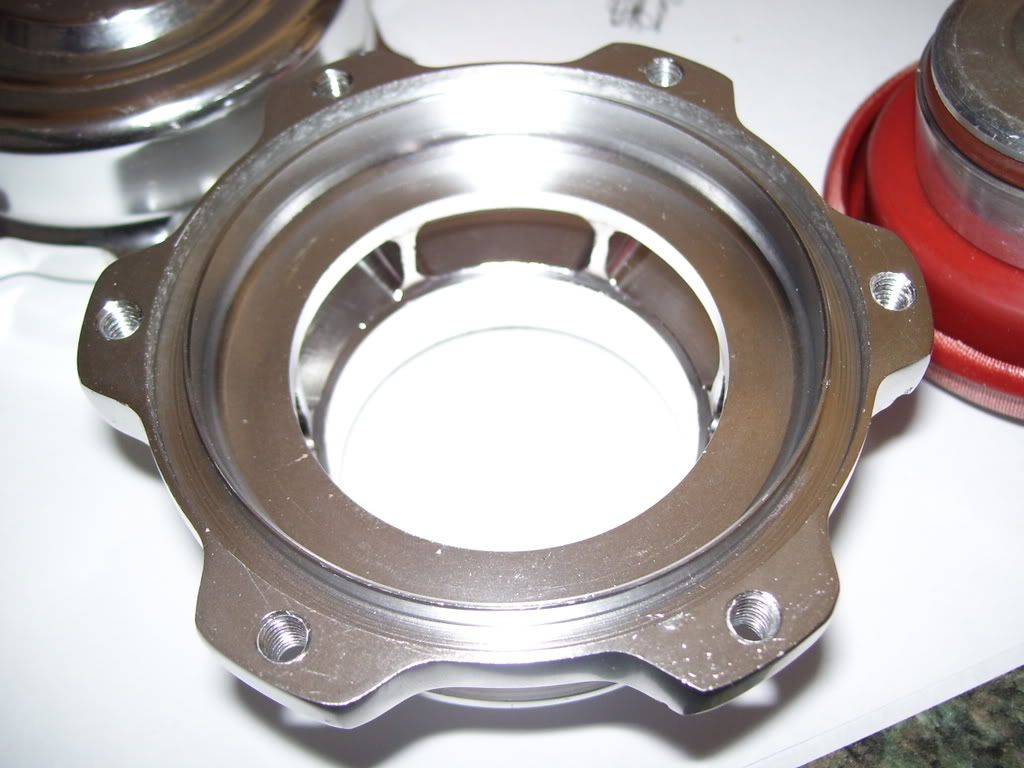



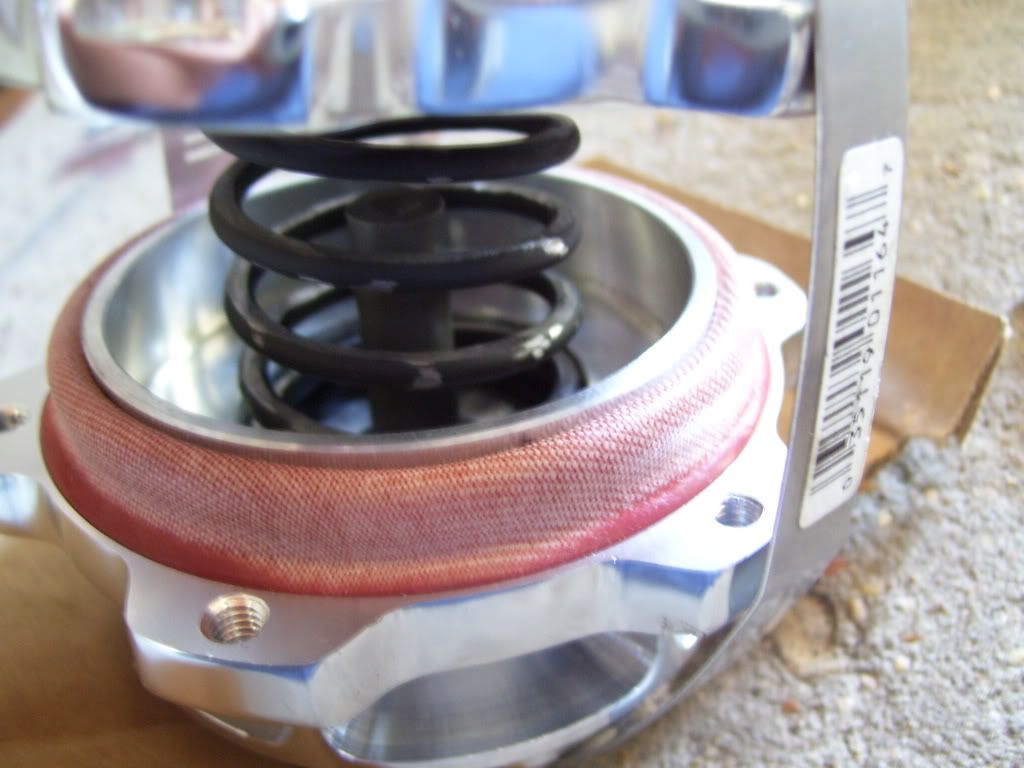
Back together

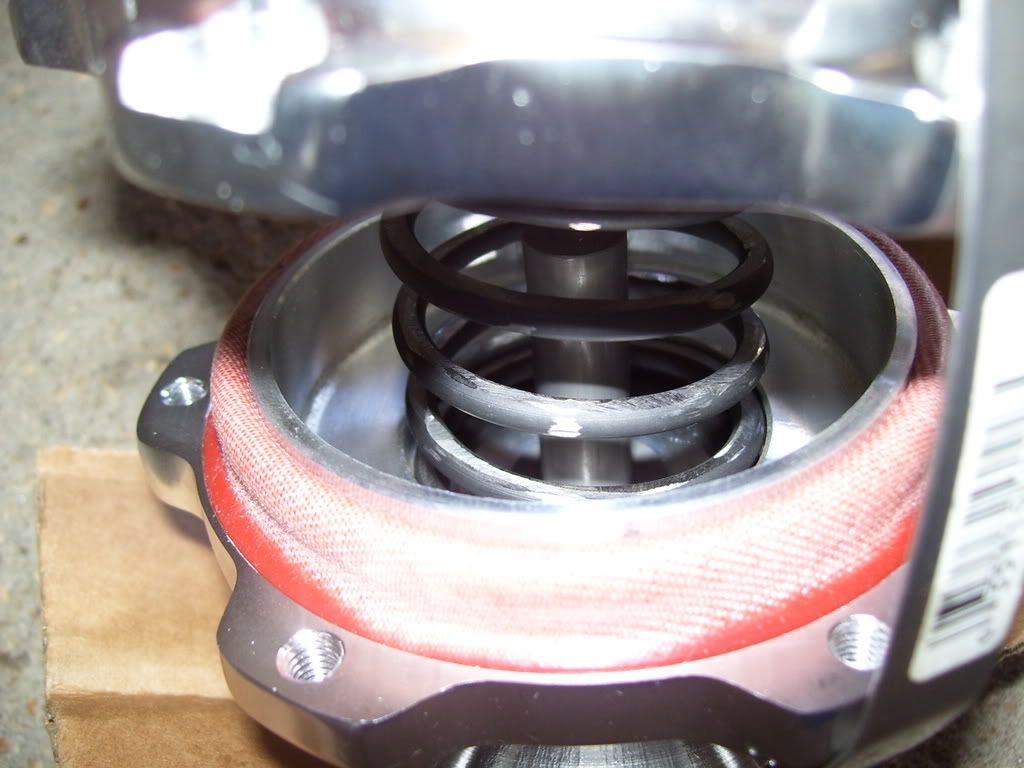
Marked the relation of the bolt to the banjo fitting. Blowing through it you can tell having it alligned it flows better.
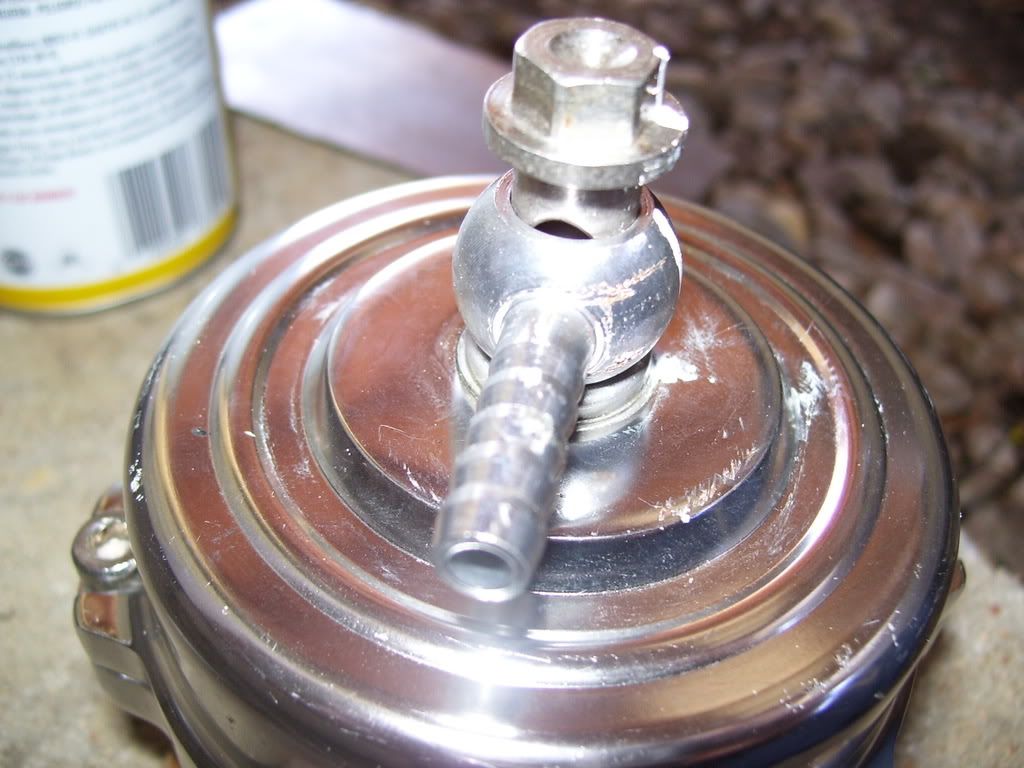

Got it installed and it's a lot better. Blows off when I shift now! Granted it's leaking a bit at idle from me grinding a bit too much off of the spring though. But I should be able to shim it and get it to stop leaking. Hope this helps someone.
Oh yeah, I'm a stealthy motherfucker so I keep it wrapped in foam to make it near-silent.
