Advantages over a kit using a plate: great hood clearance, better motor angle (better weight distribution), can use unmodded headers (some F's bolt right to your stock cat!), more "meat" left where you grind the oil pan seal for the halfshaft, more clearance for a turbo (1" more than a b-series), more clearance between the frame & crank pulley - uses stock alternator brackets, no extra-long flywheel bolts that sometimes back out, unchanged angle for slave cylinder - works just like stock.
Disadvantages: if you use OEM Accord/Prelude driver's mounts the motor will be lower on the driver's side; IAB intake manifolds may require relocating the brake proportioning valve; H/F motors with the IACV on the firewall side will require relocating or deleting the IACV. Not much else.
This can be done with just a few simple hand tools. A dremel is about the most expensive tool you'll need, but that's something no self-respecting car hobbyist should be without anyways.
Tool list:Demel or rotozip w/barrel type grinding wheels (have spares!)
hacksaw, sawzall, or bandsaw
1/2" drill bit w/hand drill or drill press
1/2" step-bit drill bit aka Unibit (HF has a 3-pc kit)
1/2" Grade 8 bolts: 6", 5", 4.5", 3.5"
1/2" Grade 8 washers (narrow SAE), lock washers, nuts
4"-6" extension bit for the step-bit
Standard tools for swaping an engine
The first thing is to get the crankshaft ground out for a b-series pilot bearing. It needs to be at least 32mm wide and over 2mm deep. I used a stubby grinding bit in a rotozip from Vermon American (from Homeboy Depot).
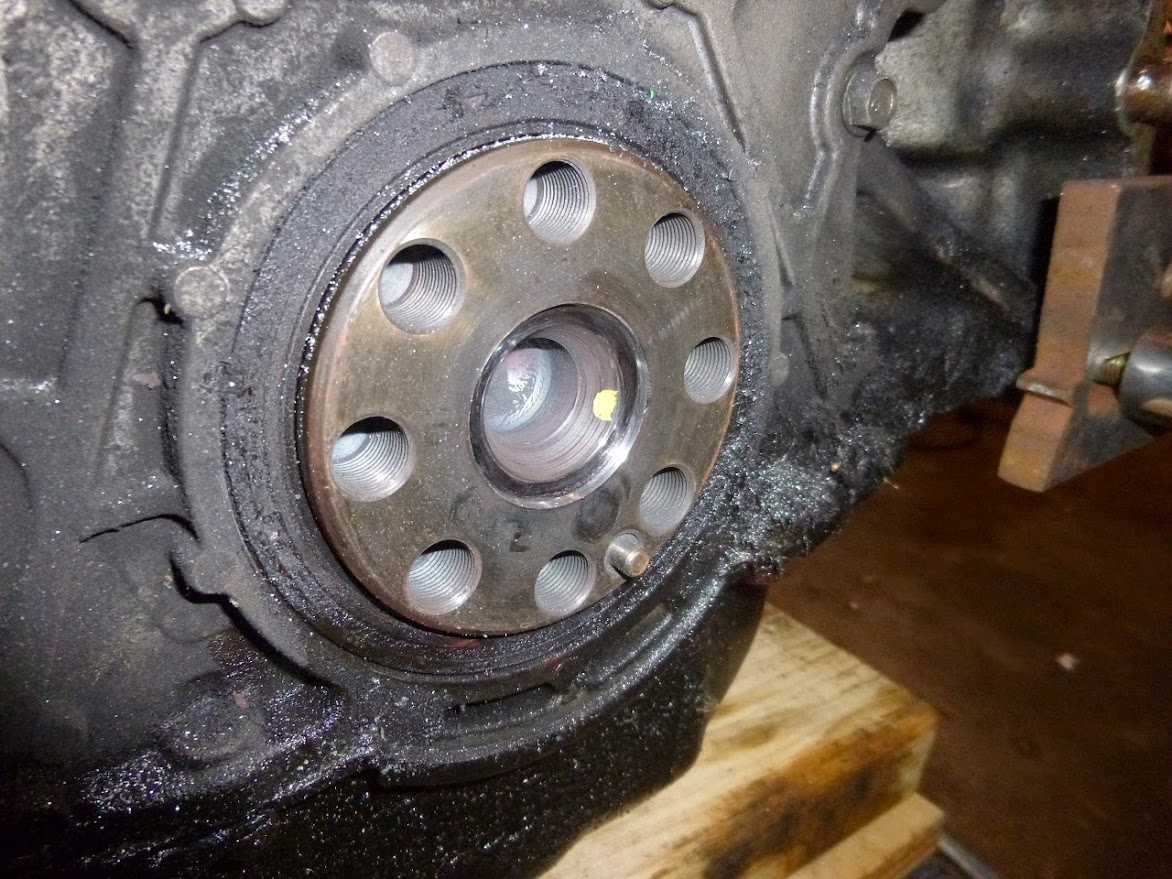
Next you have to drill the flywheel for the pin in the flywheel. You can also grind it off the crank. Beware the OEM flywheels are very hard in that area, I burned 2 bit before notching with a grinder to start the hole.
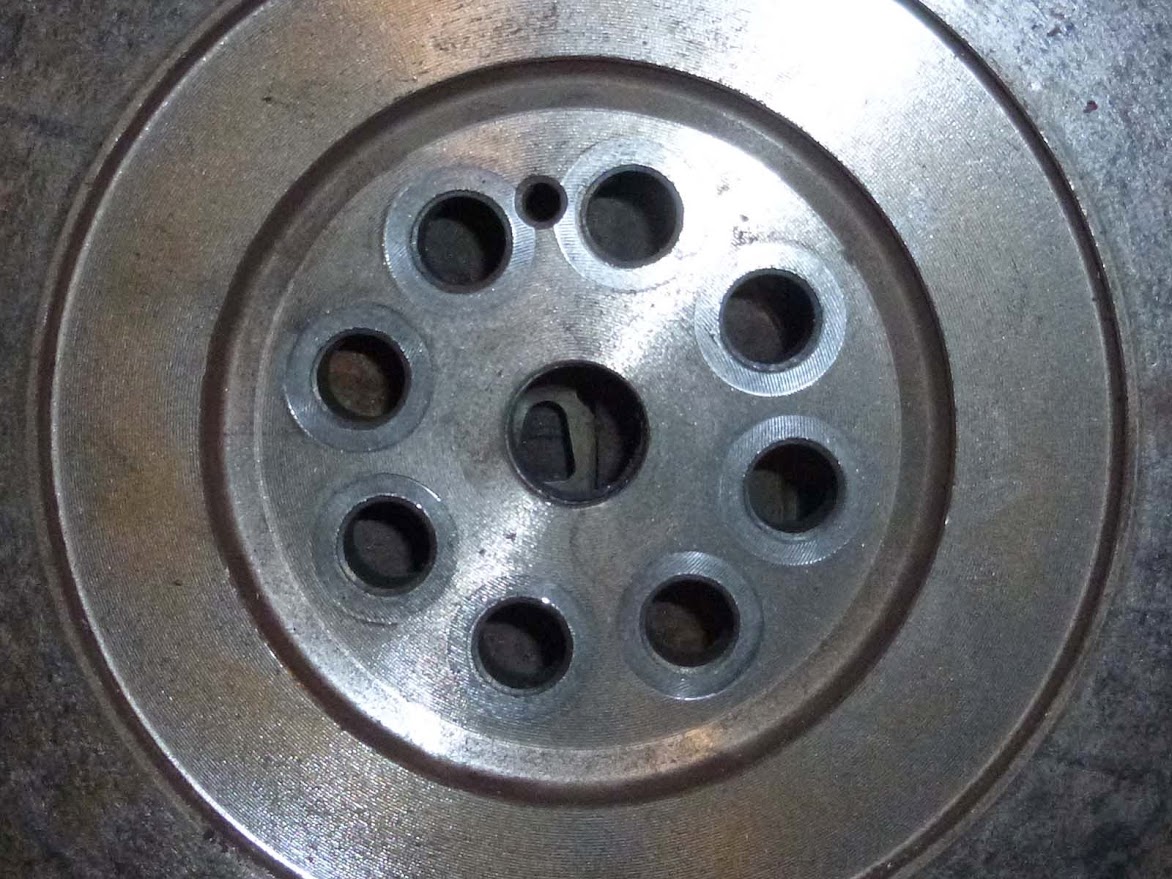
After that you enlarge the rear starter hole to 1/2". I used a step drill bit and a 1/4" hex bit extension to reach it all - make sure you start from the block side of the trans. Get creative with the bit (angle it) to slip the 1/2"x6" bolt through, or get a oversized 3-flute drill bit designed for enlarging holes in castings.
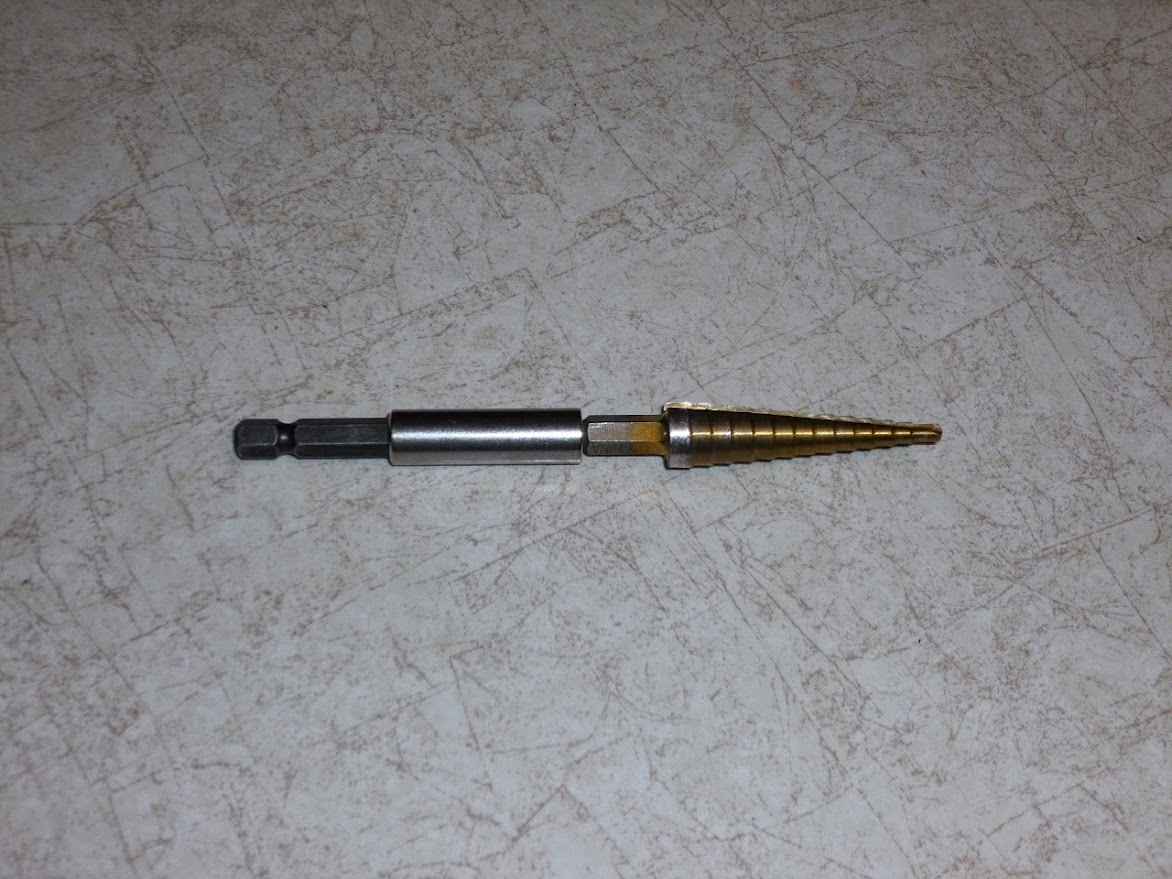
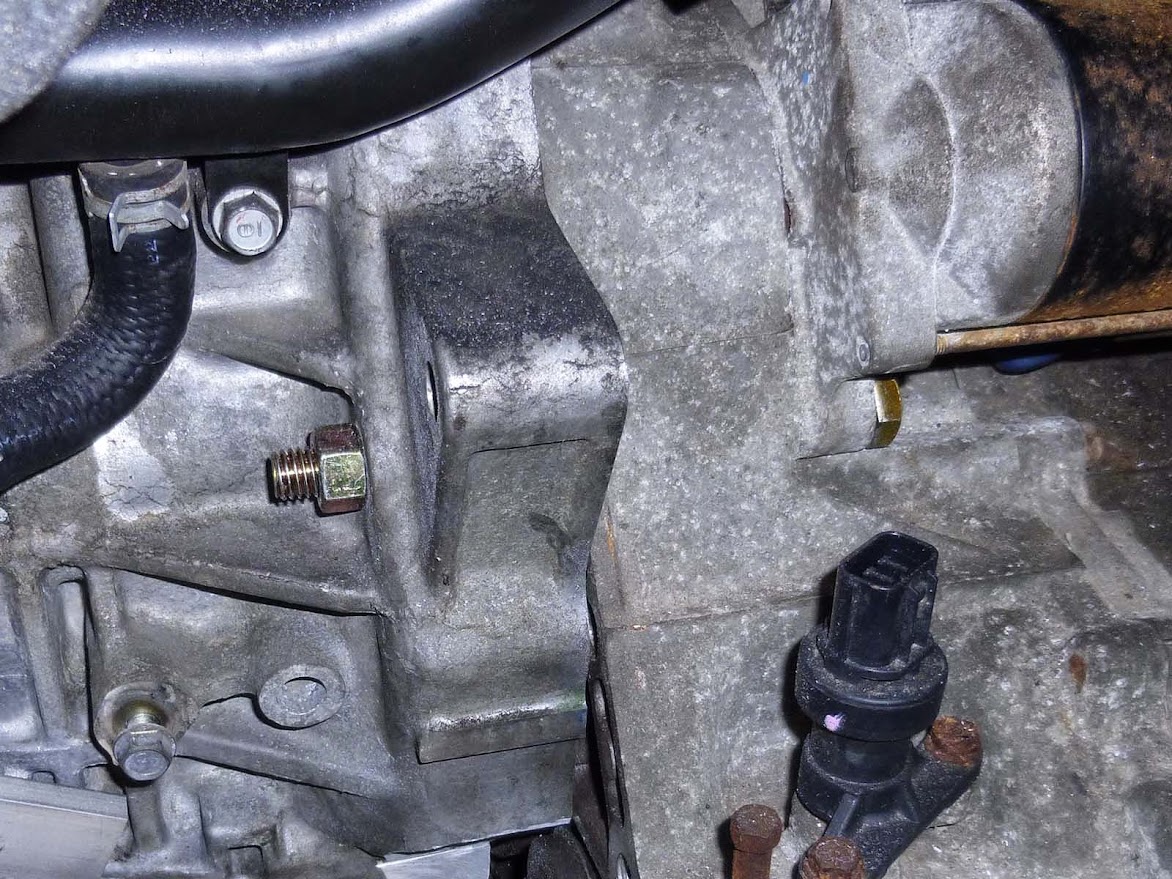
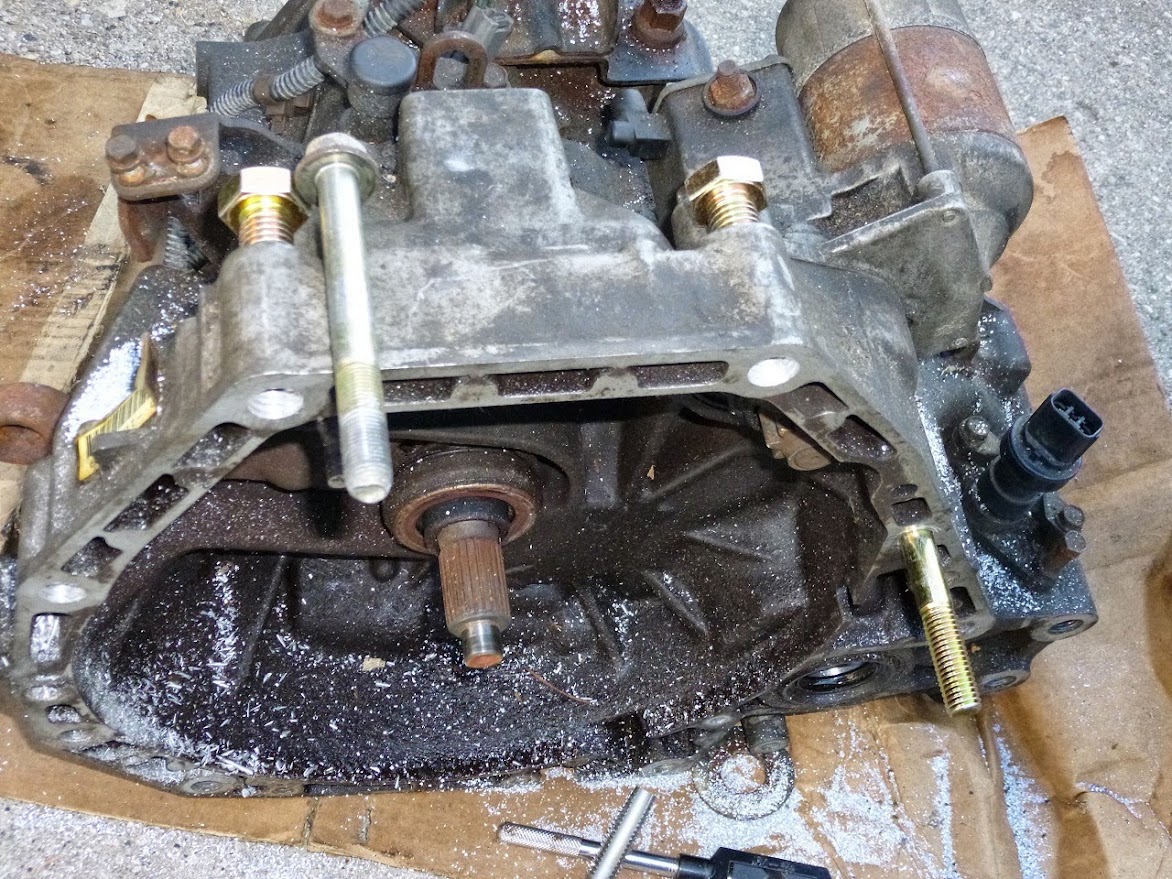
Now you can hang the trans from the block via the starter hole & pilot bearing. Drill a 1/2" hole for a 1/2"x5" bolt through the trans hole just above the clutch slave cylinder.
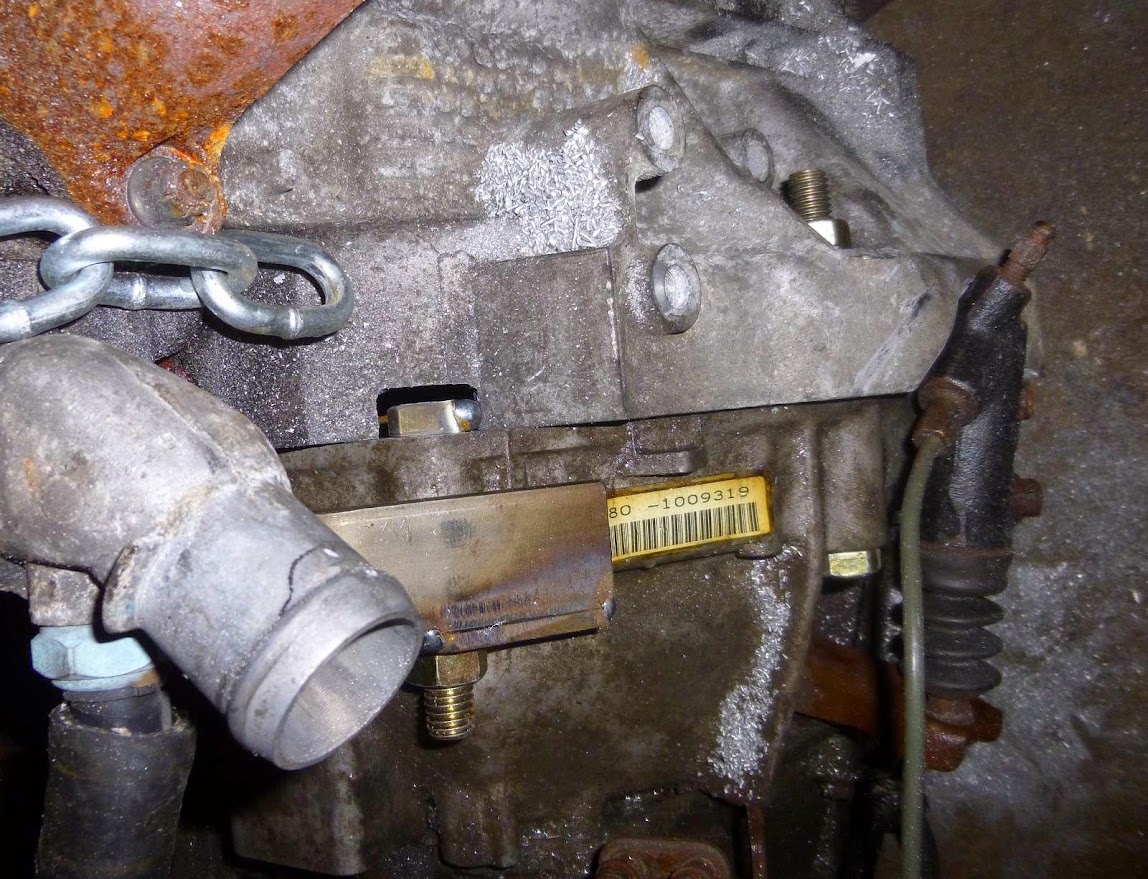
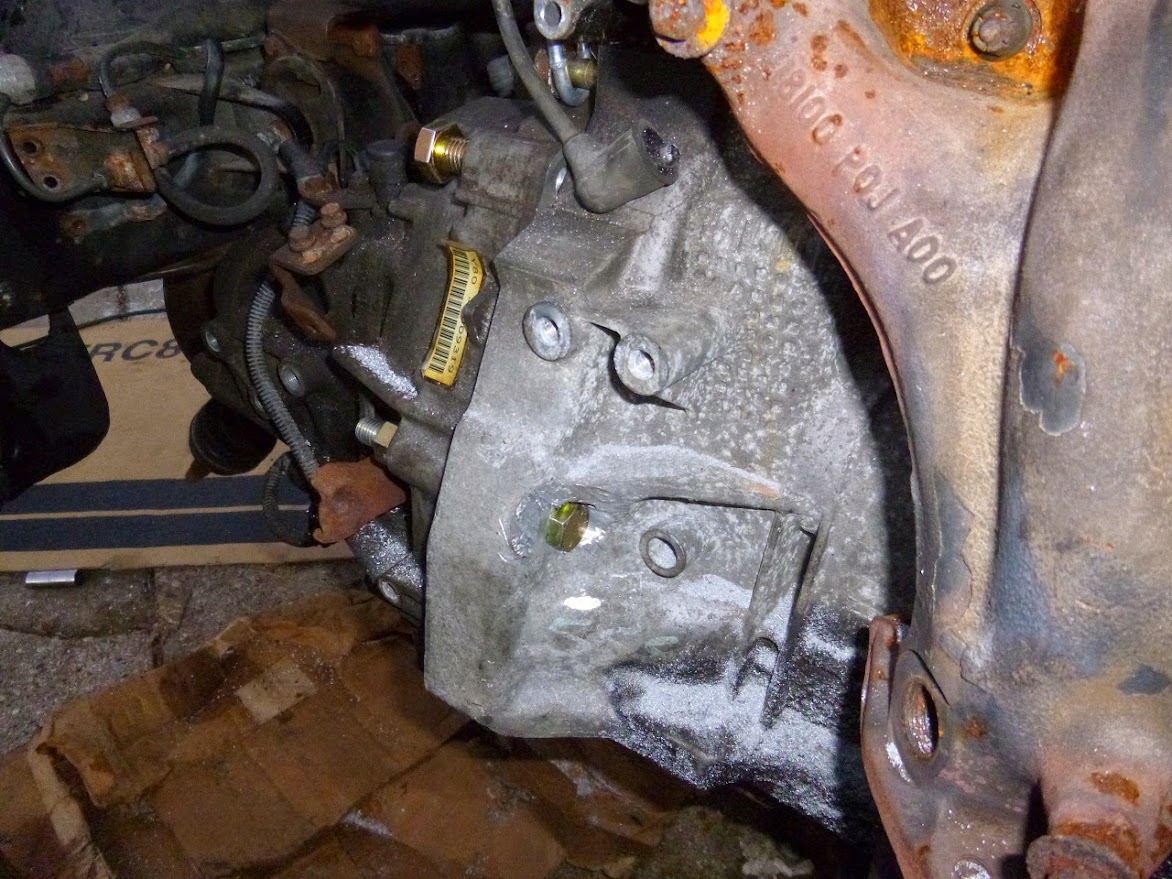

You can also work on that area to get the slave cylinder to fit. It will take some time, but the pics should give you a good start.
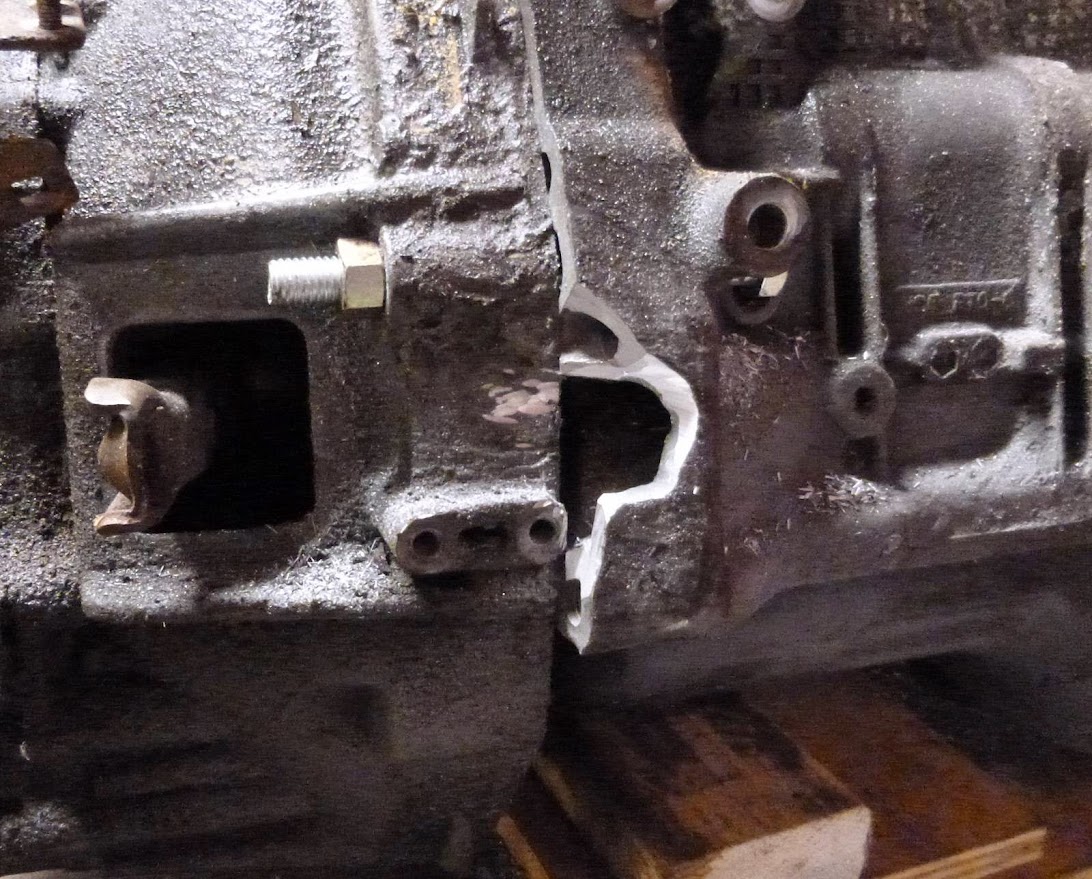
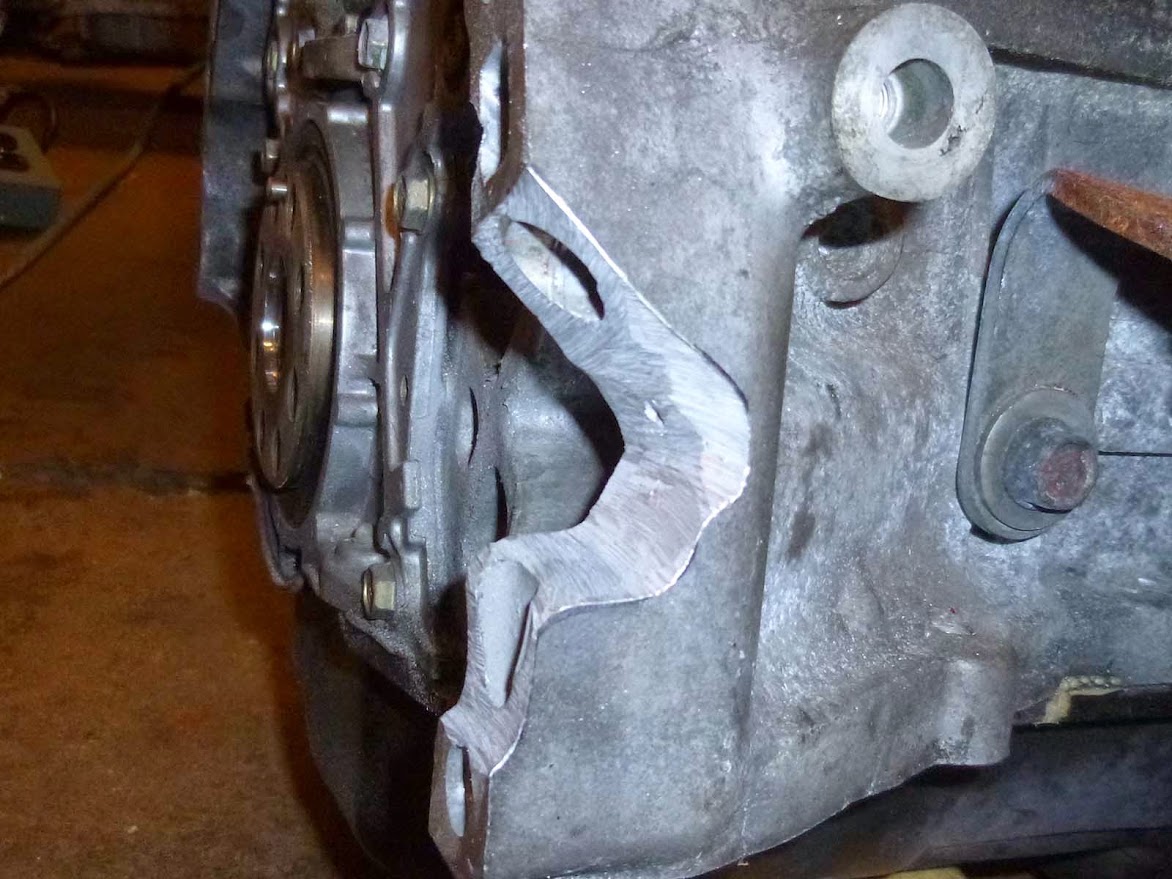
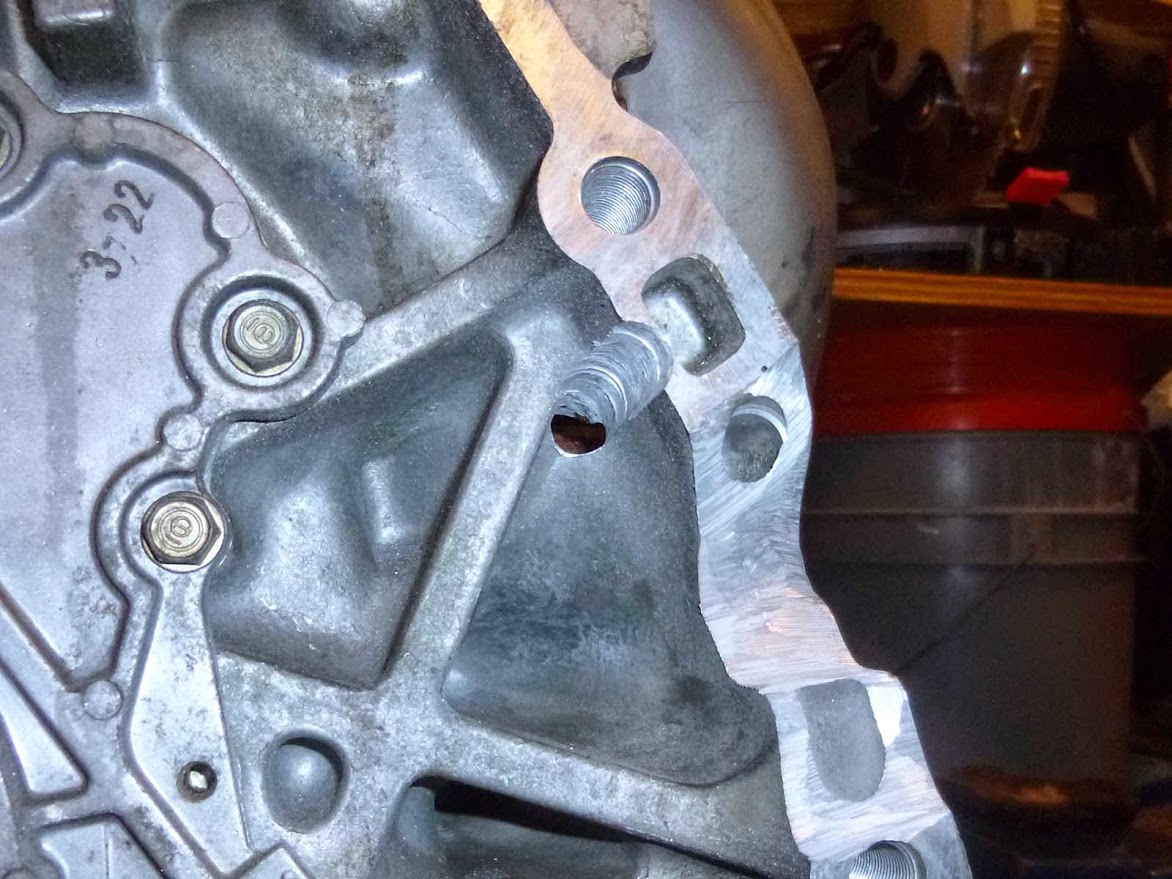
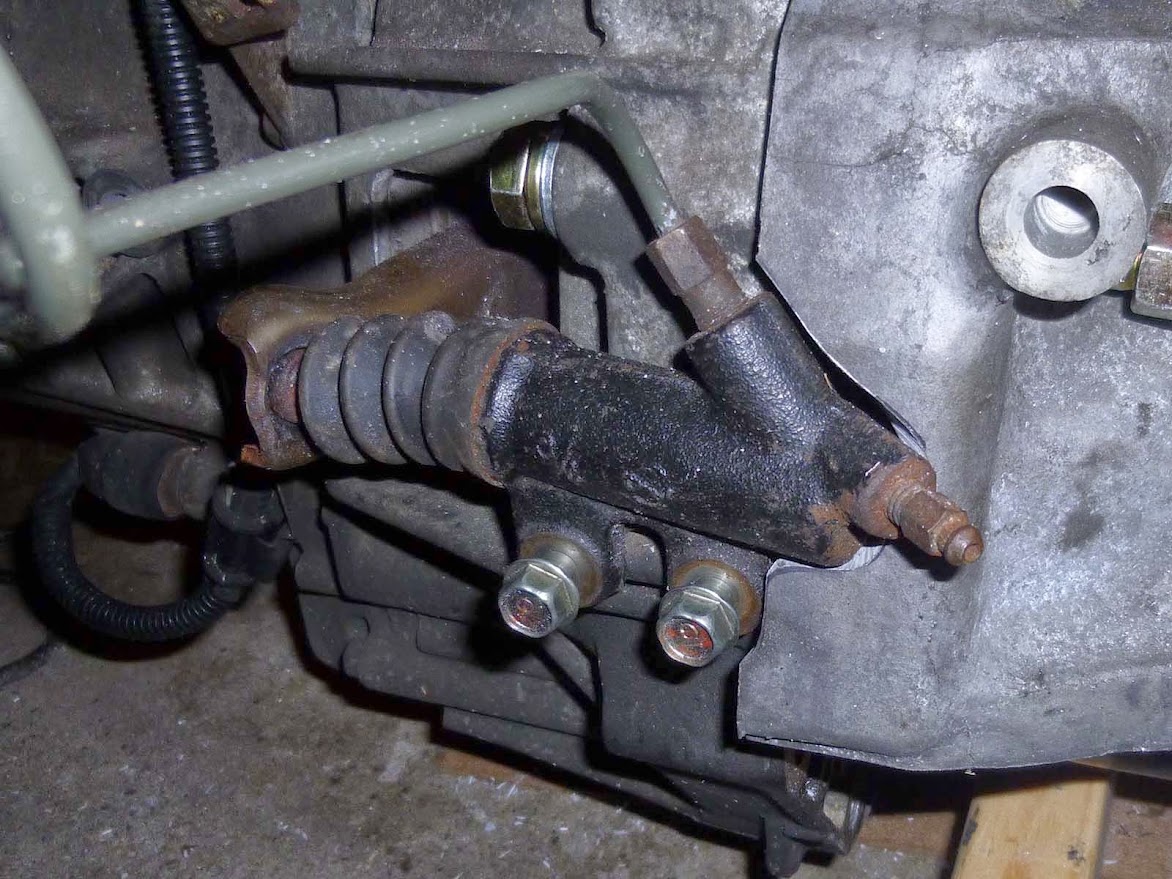
You can move up to the block stamp. You need to cut the window a bit longer (downwards) by 1/4". If it's a newer F-series, it may not even have a timing window. Cut it large enough to fit the open tip of a 3/4" box wrench into it.
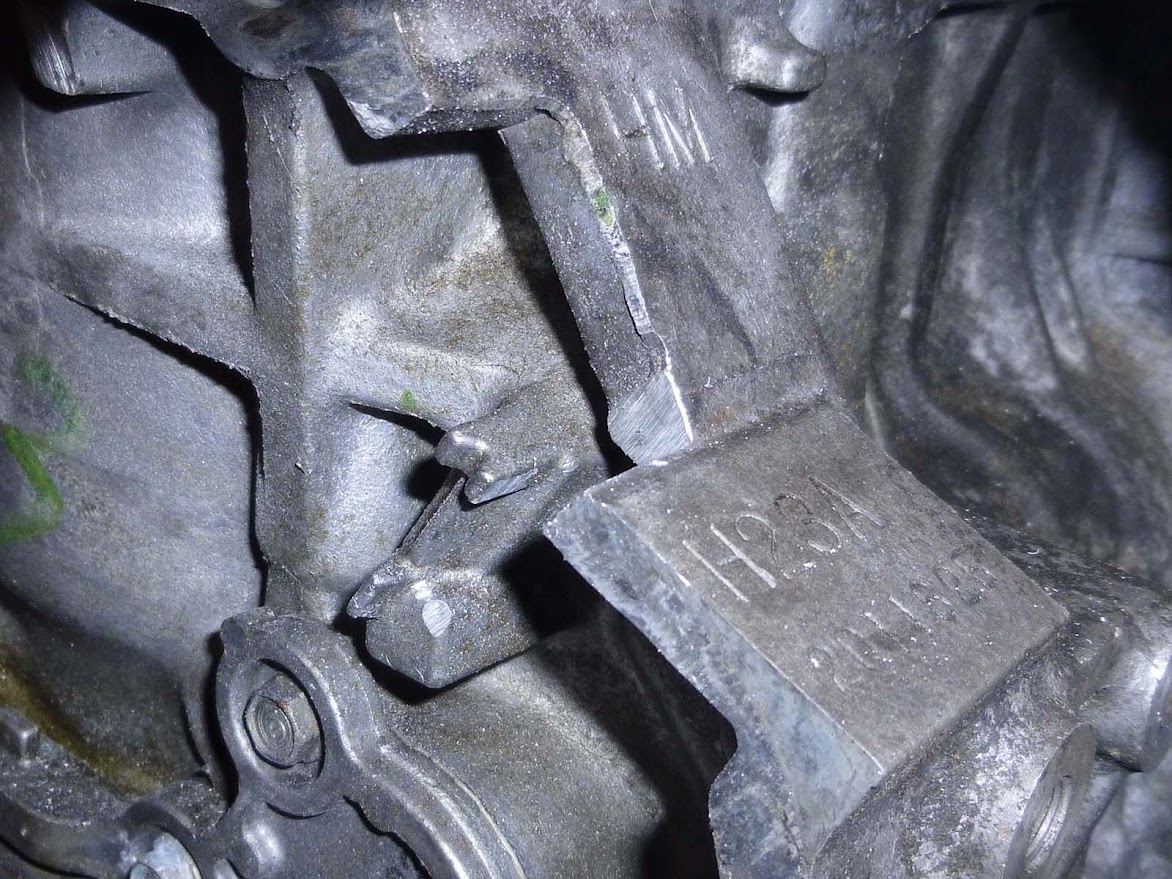
You need to do some more grinding behind the window. There is a knob/pin that sticks out and needs to be shaved. Beyond that the block webbing between the two top holes needs to be removed a bit, especially on H22/H23/F23 blocks. This gives the bolt through the trans a place to sit. If done right it also keeps it from spinning.

