Some more updates:
I replaced the stock clutch master with a S2k unit w/ spacer.

Take the old one out.

Put the S2k unit in with spacer and you will notice the hydraulic line does not line up well.
No problem with a little patience use your hands to gently bend and pull the line to line up with the new cylinder.

Make sure you have the rod adjustment all the way out before connecting it to the clutch peddle.

Bleed the clutch hydraulic system, should take ya about 30min. for the total install

Before this clutch master cylinder replacement I would have to sit closer to the dash.
I would have to use a lot of leg movement to engage/disengage the clutch.
Now I can put my seat back further and drive more comfortably, use 1/3 the leg movement.
Peddle is firmer and I have enough movement to preload the clutch to hold my car on hills.
I can also shift a lot faster.
Since I'm putting the He351ve on, I better get the oil pan tapped for oil return.
Chose to have the return come in above the baffle and in between reinforcement ribs of the pan.


I was looking for an aluminum 1/2" or larger tube for the return.
Then I remembered the line to the old a/c condenser I have laying around.

Positioned the line pointing to center and up, while making sure it is in no position to make it hard to tighten the oil pan to block fasteners.

The new engine setup:
Y8 block
75.5mm Vitaras
Cunningham Rods
A6 crank
y8 oil pump
Y8 head mildly ported by me
Stock y8 cam with adjustable gear
stock valves with crower springs and retainers
Block was bored 0.5mm over and decked 0.020"

Using the y8 timing components, except at the crank.
The A6 crank is the older smaller snout crank.
So I have to use timing belt sprocket from the a6 and harmonic balancer/pulley.

With the crank and short block assembled the crank turns nice with light effort.

The inside of the oil pan needed a little cleaning.
Make it easier when the pan has a bolt in baffle.


Notice how close the turbo oil drain is to above the baffle.

Put the oil pan on and look how the oil return clears, the block and leaves plenty of room to bolt up the pan.

Put the head on and proceeded to get the head studs in and noticed that all of the studs are too long.
Not one or two of them, but all of them. I bought these of a nog on here and I think they sent me the wrong one.
I double check and made sure the machinist took off 0.020" of the deck and not 0.200" off.
The vitara piston top sits ~0.065" below deck, like it should.
So went to the hardware store and bought a box of 100 L9 washers and used 5 washers/stud and torque everything down.
Got the timing belt on with all the timing marks lined up. By the way the A6 crank has now marks to I used a sharpe to mark TDC.
Later I'll mark the pulley with a hacksaw blade to make it easier to time with a light.
Hand crank the engine over and it is freaking hard as hell.

So take the rocker assembly off and inspect the cam, it had some serious divots in a couple of the lobes.
So I grab another cam I have laying around looks to be a z6 cam.
Then I thought I better check the rocker assembly found at least 4 rockers with flat/worn pads.
I have 3 z6 and 2 y8 rocker assemblies so I'll just use the best of what I have.

Strip the rocker shafts and there is a bit of metal clogging up the exhaust rocker shaft.


They should have clean holes like this.

By the way P08 (z6) and P2a (y8) rocker shaft are not exactly the same


With everything stripped and clean I start from the dizzy side, and start assembling everything together.



Here is another note, if you want to know if you have P08 parts in your y8 look at the pad on the rockers.
The y8 pads have little notches on them. The pad on the right is a po8

Got the head back together and bolted on, hand cranked the long block, a lot easier now.

Got the water pipe back on with black box, and a Tuner Toy oil feed fixture. I bought from a nog on here new.

Probably going to use a copper 1/8" hard line for the oil supply.


So time to bolt the S/C on, this time with a new idler pulley and lower bracket bolt setup.
Last year when I went to the PNW RHMT meet, I kept losing belts, and could not get above 7psi on the dyno.
Well the bottom bracket rear most bolt (from pulley) had fallen out.
I decided to not repeat this issue, got me a 3/8 x 8" bolt with nylock nut and new 90mm dia. idler pulley.

That fixed, I bolted on the partially done Wier log manifold on to figure out turbo placement.
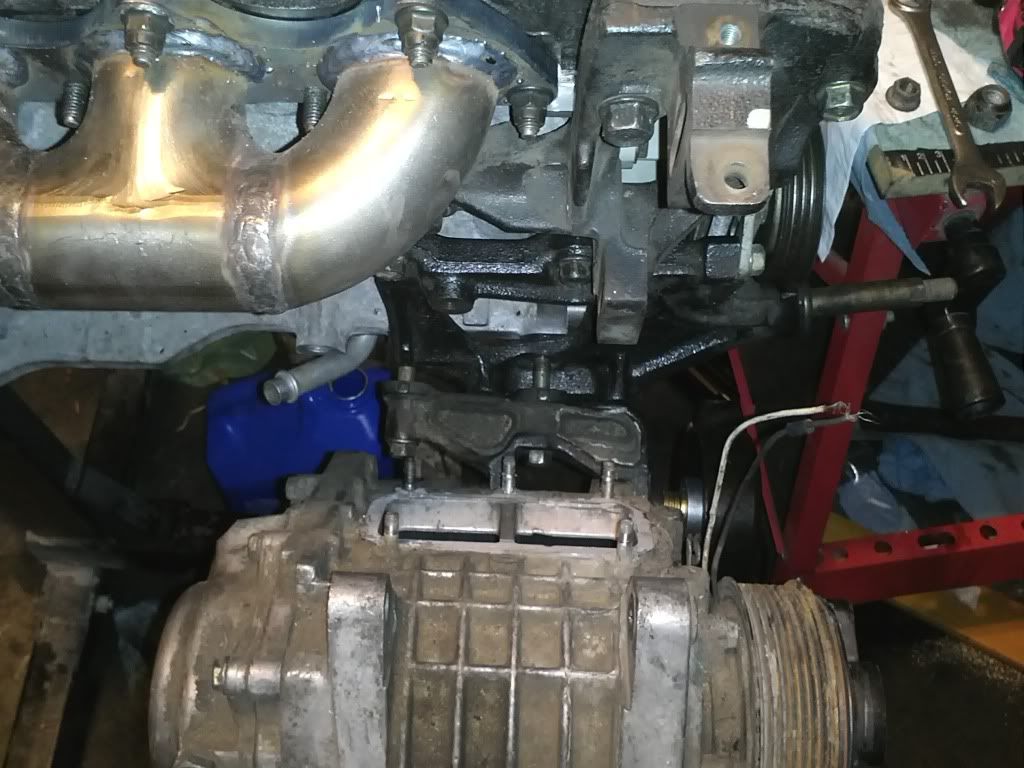
He351ve sits nice and snug above the s/c, with the turbo compressor housing laying top of the s/c.

This is all I have for now will have more updates soon.
